The warehouse sector is undergoing a remarkable evolution. As online shopping grows at unprecedented rates, the demands placed on pick and pack warehousing have intensified significantly. What was once a straightforward operation now requires sophisticated systems to meet consumer expectations for rapid, accurate delivery.
The future of pick and pack is increasingly defined by technological advancement, data integration, and automation. These changes bring both challenges and opportunities for eCommerce businesses wanting to remain competitive in a fast-changing environment.
What Is Pick and Pack Warehousing?
Pick and pack warehousing forms the backbone of modern order fulfilment. It is the methodical process where warehouse staff select items from inventory (picking) and prepare them for shipment (packing) based on customer orders.
The workflow typically includes receiving inventory, picking products from storage locations, packing orders with appropriate materials, and dispatching parcels to customers. This process sits at the heart of the fulfilment chain, connecting inventory management with the final delivery experience.
For retail brands, efficient pick-and-pack warehouse solutions directly impact customer satisfaction, return rates, and delivery times. When executed well, customers receive exactly what they ordered, in good condition and within the promised timeframe. When things go wrong, the consequences often include costly returns and a damaged brand reputation.
Why Is The Pick And Pack Industry evolving So Fast?
Several factors are converging to drive the rapid transformation of pick-and-pack warehousing. Online retail growth has created unprecedented demand for warehouse space and services, putting pressure on facilities to process more orders in less time.
Consumer expectations have fundamentally changed too. Next-day and same-day delivery are now standard rather than premium offerings. Businesses also need to manage inventory across multiple platforms, which requires close coordination between digital systems and physical stock.
For UK businesses in particular, post-Brexit regulations have introduced new complexities in international shipping. Customs documentation, VAT considerations, and compliance requirements now play a larger role than ever in warehousing operations.
The global warehousing and storage market is projected to reach $869.32 billion by 2025, highlighting the enormous scale and importance of the sector.
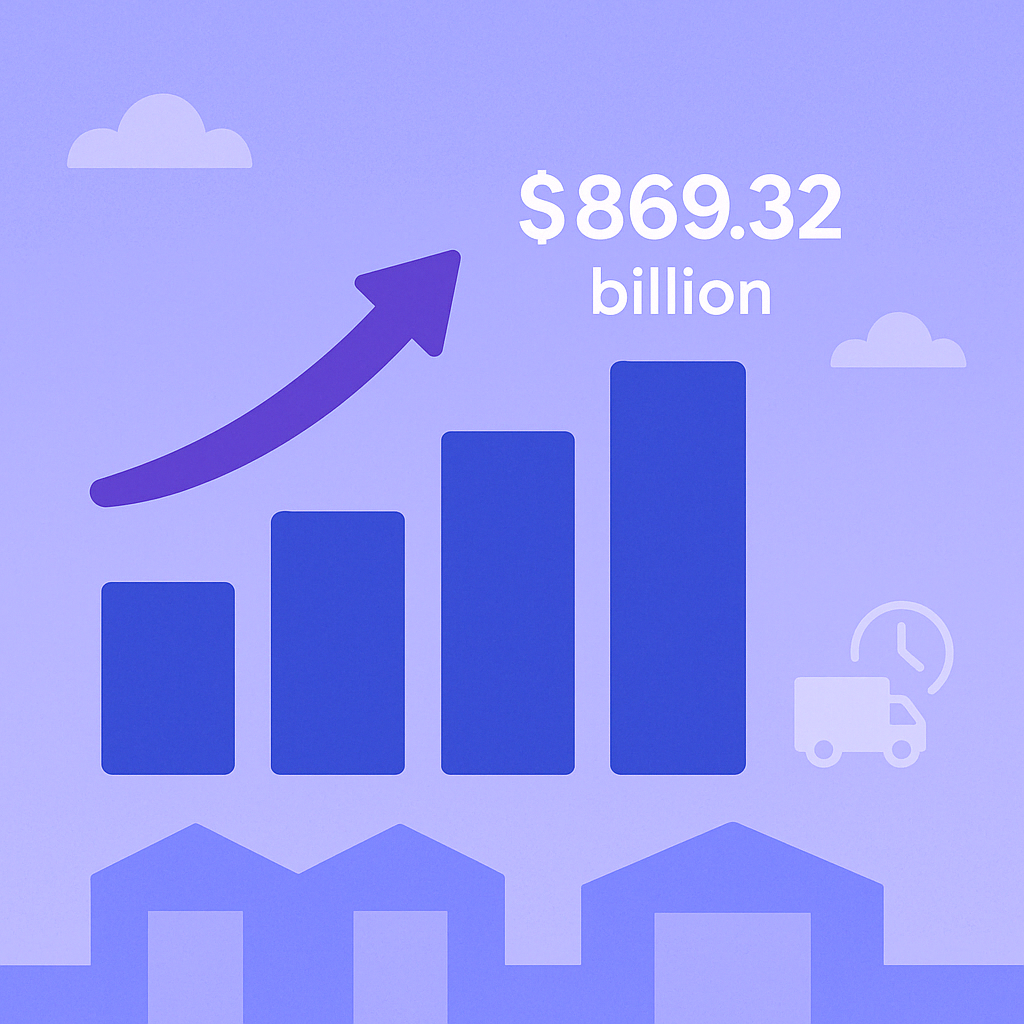
Key Trends Shaping the Future of Pick and Pack
Innovations in technology are being adopted to help warehouses keep pace with growing demand and increasing complexity. These advancements bring greater accuracy, scalability, and efficiency to modern fulfilment operations.
Automation in Warehousing
Automation is one of the most transformative trends in pick and pack logistics. Robotic and mechanical systems can now perform repetitive warehouse tasks with incredible precision and consistency.
Some examples include:
- Robotic picking arms that handle 4 to 6 times more orders per hour than humans, with error rates reduced by over 99%
- Advanced conveyor systems that transport items across vast warehouse spaces
- Automated Storage and Retrieval Systems (AS/RS) that maximise space by managing high-density vertical storage
- Voice-directed picking, allowing workers to receive instructions through headsets and work hands-free
- Collaborative robots (cobots) that support human staff by taking over repetitive physical movements
AI and Machine Learning in Order Fulfilment
Artificial intelligence is redefining how warehouses manage stock and respond to customer demand. Machine learning algorithms help teams make accurate forecasts and operate more efficiently.
AI-driven systems can analyse historical data alongside seasonal trends, marketing campaigns, and even weather patterns to predict order volumes. Neural networks optimise where stock is placed in the warehouse to reduce travel time during picking. Computer vision systems identify damaged products and verify selections in real time, reducing the likelihood of errors before items are shipped.
In addition, these technologies enable continuous performance monitoring and process improvement by identifying inefficiencies that human managers might miss.
Real-Time Data and Integration
Modern pick-and-pack operations rely heavily on the seamless flow of real-time data between platforms. Orders from sites like Shopify, Amazon, and eBay can be automatically routed into fulfilment systems with zero manual intervention when integration works correctly.
Technologies driving this include:
- API connections that remove manual data entry
- Iot sensors track inventory levels, equipment status, and warehouse conditions
- Digital twin technology: virtual replicas of physical warehouses used to test layout or process changes without disrupting live operations
These tools provide instant visibility and control, which is especially useful during peak seasons or when scaling operations.
Eco-Conscious Packaging and Operations
Sustainability is a rising priority across the supply chain. Warehouses are adopting eco-conscious practices to reduce waste and cut emissions while maintaining efficiency.
Steps being taken include:
- Right-sized packaging algorithms that reduce excess materials and lower shipping costs
- Energy-efficient lighting and climate systems
- Integration of renewable energy sources, such as solar panels
- Automated systems that reduce errors, returns, and waste across operations
Sustainability improvements can often align with cost savings, making them a practical investment as well as an ethical one.
Challenges and Opportunities Ahead
The road ahead is promising but not without friction. Businesses face key challenges that must be addressed to take full advantage of future opportunities.
Labour recruitment and retention remain difficult across the logistics sector. While automation can help alleviate the pressure, businesses still need trained staff to manage complex operations and technologies. Meanwhile, nearly 40 per cent of warehouses report issues related to space and staffing shortages.
Delivery speed continues to accelerate, yet this must be balanced against environmental considerations and rising operational costs. Implementing new technologies can be expensive, particularly for smaller businesses. For these companies, deciding which innovations deliver the best return on investment is essential.
Managing inventory across different sales channels, each with its own interface and process, also adds complexity. Recent global events, including supply chain disruptions and pandemics, have underscored the need for flexible and resilient warehouse operations.
How eCommerce Businesses Can Prepare
Reassess Your Current Fulfilment Workflow
To future-proof operations, start with a clear understanding of where your business currently stands. Review your fulfilment process and identify bottlenecks:
- Are delays most common during receiving, picking, packing, or dispatch?
- What does your data say about accuracy, processing times, and return reasons?
Also consider how your current systems would cope if order volumes doubled, whether due to peak trading periods or expansion.
Evaluate Technology Partners
Look for fulfilment technology that is scalable and integrates smoothly with your existing setup. Key capabilities to prioritise include:
- Strong API connectivity with sales and inventory platforms
- Real-time data sharing and analytics
- The flexibility to support both current and future growth
The ability to gain immediate visibility over stock levels, order statuses, and warehouse performance is no longer a nice-to-have; it is essential.
Choose a Future-Proof Fulfilment Partner
If you are exploring outsourcing options, the right fulfilment partner can offer a major operational advantage.
Cloud Fulfilment is a strong choice for growing eCommerce brands because:
- They have an in-house IT team dedicated to developing and refining fulfilment technology
- Their system integrates with all major eCommerce platforms, supporting seamless multichannel fulfilment
- They have experience with specialised categories like fashion, health, and beauty
- As part of the Parcel Monkey Group, they offer competitive international shipping rates through a vast courier network
Security, compliance, and data protection are also built into their operations, which are important considerations for brands planning to scale.
Embracing the Future of Pick and Pack
The warehousing industry is entering a new era. Customer expectations are rising, competition is increasing, and technology is rapidly reshaping how fulfilment works.
Operations that integrate automation, real-time data, and smart systems with human expertise will gain a distinct advantage – the result: greater speed, lower costs, improved accuracy, and happier customers.
For ambitious eCommerce brands, the message is clear. Fulfilment innovation is not just about adapting to trends; it’s about setting your business up for sustainable, long-term success.
FAQS: The Future of Pick and Pack Warehousing
What is the difference between traditional and automated pick and pack systems?
Traditional systems rely on manual processes, while automated solutions use robotics and digital tools to handle tasks more quickly and accurately. Automation tends to offer better speed and scalability over time.
How much does it cost to automate a pick and pack warehouse?
It depends on the size and complexity of the operation. Basic automation might cost a few thousand pounds, while end-to-end robotic systems can require millions. Many businesses start small and gradually scale up.
Can small eCommerce businesses benefit from automated pick and pack solutions?
Yes. Even small operations can implement modular automation to solve specific issues. Working with a fulfilment partner who already uses advanced systems is another cost-effective way to benefit from automation.
What role does warehouse layout play in pick and pack efficiency?
An optimised layout can cut picker travel time by 30 to 40 per cent. Frequently ordered items should be placed in a convenient location, and workflows should flow logically from picking to packing and dispatch.
How does pick and pack fulfilment impact customer experience?
Accurate picking, secure packing, and fast shipping all directly affect whether a customer is satisfied or not. Efficient fulfilment helps reduce returns and encourages repeat purchases.
What should I look for in a pick-and-pack software system?
Focus on features like real-time inventory tracking, sales channel integration, mobile accessibility, and automation tools. Ease of use and good vendor support are also important for long-term success.