Article Takeaways
- Optimising the pick and pack process reduces costs and improves accuracy
- Choosing the right picking method (piece, batch, zone, or wave) enhances efficiency.
- A strategic warehouse layout and inventory slotting speed up fulfilment.
- Technology like barcode scanning and WMS boosts accuracy and productivity.
- Proper packing stations and quality control prevent errors and damage.
- Measuring key performance indicators helps refine processes over time.
- Outsourcing to a 3PL enables scalability and operational flexibility.
In the world of eCommerce and order fulfilment, picking and packing best practices can make the difference between thriving and merely surviving. The process of selecting products from inventory and preparing them for shipment might seem straightforward, but it represents a critical operation that demands attention and optimisation.
Research indicates that warehouse picking accounts for approximately 55% of distribution centre operating costs, making it a prime target for efficiency improvements. By refining your pick and pack process, you can significantly reduce costs, improve accuracy, and most importantly, increase customer satisfaction.
For high-growth businesses, implementing optimised pick and pack systems isn’t just about saving time; it’s about creating a competitive advantage that allows for scalability while maintaining quality service. Cloud Fulfilment, with its scalable and affordable e-commerce fulfilment solutions, specialises in helping businesses achieve this balance through streamlined picking and packing procedures that adapt to growth without compromising on performance, and allow for end-to-end pick, pack, and distribution.
What is Pick and Pack and Why Does it Matter?
The pick and pack process forms the backbone of order fulfilment, connecting the dots between receiving inventory and shipping products to customers. When a customer places an order, warehouse staff select (pick) the correct items from storage locations and then prepare (pack) them appropriately for shipping.
This workflow might sound simple, but its execution directly impacts both operational efficiency and customer experience. According to logistics industry data, inefficient pick and pack operations can account for up to 70% of warehouse labour costs, highlighting the financial implications of poorly optimised processes.
With today’s consumers expecting increasingly rapid delivery times, often next-day or even same-day, warehouses face mounting pressure to process orders quickly and accurately. A well-designed pick-and-pack workflow allows businesses to meet these expectations while maintaining cost control.
The ripple effects of inefficient procedures extend beyond just operational costs. Late deliveries, incorrect orders, and damaged products resulting from suboptimal picking and packing can damage brand reputation and lead to lost customers. Our dedicated picking and packing services are designed to prevent these issues through systematic, reliable processes.
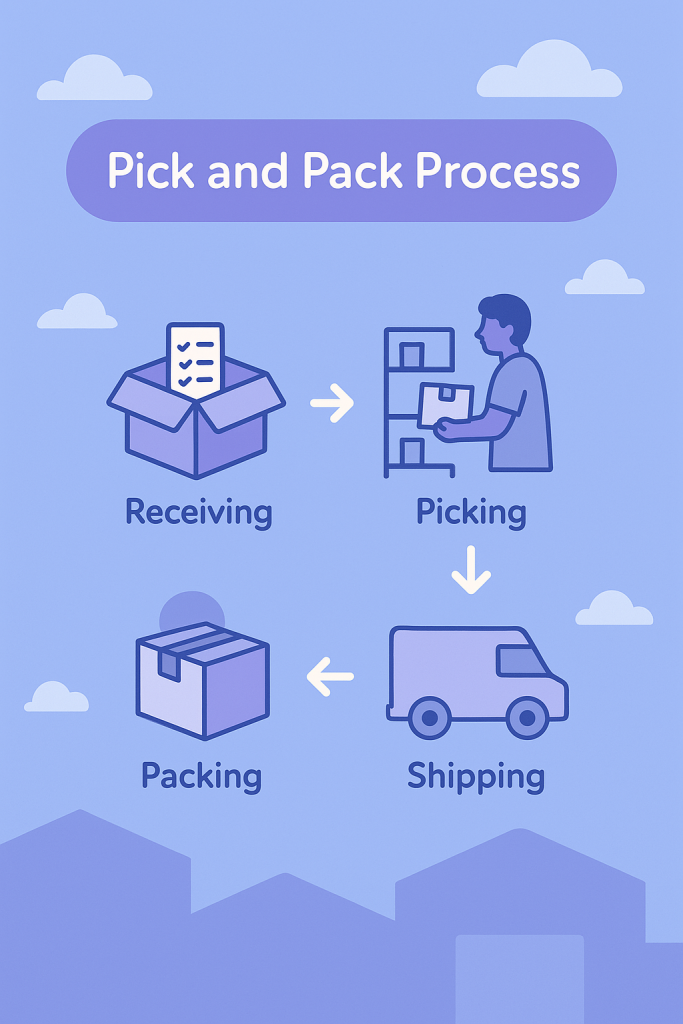
Understanding Different Pick and Pack Methods
Choosing the right pick and pack methods for your business depends on various factors including order volume, inventory diversity, and available resources. Each approach offers distinct advantages and is suited to different operational environments.
Piece Picking
Piece picking (sometimes called discrete picking) involves fulfilling one order at a time. A warehouse worker collects all items for a single order before moving on to the next. This method works well for:
- Small businesses with low order volumes
- Companies with a limited product catalogue
- Operations requiring high levels of order customisation
While piece picking offers simplicity and reduces errors, it becomes inefficient as order volumes increase.
Batch Picking
With batch picking, workers collect items for multiple orders simultaneously, grouping similar products to reduce travel time within the warehouse. This approach is ideal for:
- Medium-sized businesses with growing order volumes
- Companies with moderate product diversity
- Operations where multiple orders often contain the same items
By reducing walking time between locations, batch picking can improve efficiency compared to piece picking.
<H3> Zone Picking
Zone picking divides the warehouse into sections, with specific staff assigned to each zone. As orders progress through the warehouse, each zone picker adds the relevant items before passing the order to the next zone. This method is suited for:
- Larger operations with high-order volumes
- Warehouses with clearly defined storage areas
- Businesses with diverse product catalogues requiring specialised handling
Zone arrangements in warehouse picking and packing create a more organised workflow, allowing staff to become experts in their assigned areas.
Wave Picking
Wave picking combines elements of batch and zone picking, releasing groups of orders to be fulfilled during scheduled “waves” throughout the day. This sophisticated approach works best for:
- High-volume operations processing thousands of orders daily
- Warehouses with complex inventory management needs
- Businesses requiring precise shipping schedule coordination
The flexibility of wave picking allows for adaptation to changing priorities and workloads, making it popular among advanced 3PL pick and pack providers.
Selecting the appropriate method depends on specific needs and operational scale. Our warehousing solutions are designed to accommodate these different approaches, tailoring the pick and pack logistics to business requirements.
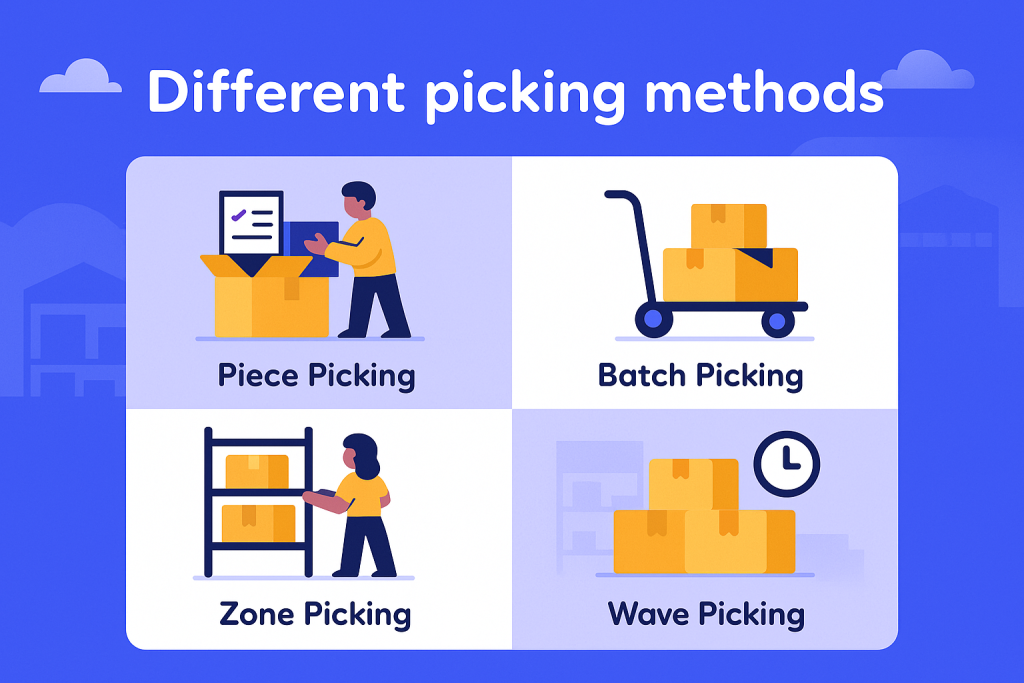
Warehouse Organisation for Optimal Pick and Pack Flow
The physical layout and organisation of your pick-and-pack warehouse play a crucial role in operational efficiency. A well-designed warehouse can reduce travel time, minimise errors, and increase throughput.
Strategic Warehouse Layout
Organise your warehouse based on the natural flow of inventory through each functional area:
- Receiving and inspection
- Storage and putaway
- Picking zones
- Packing stations
- Shipping area
This logical progression eliminates backtracking and creates a streamlined path for orders to follow. Clear signage and floor markings help staff navigate efficiently, especially important in larger pick-and-pack warehouse UK facilities.
Inventory Slotting Strategies
How you position inventory within your warehouse significantly impacts picking efficiency:
- Volume-based slotting: Place fast-moving items closest to packing areas to reduce travel distance for your most common picks.
- Class-based slotting: Group products with similar handling requirements together.
- Complementary slotting: Position items frequently ordered together in proximity to reduce picking time.
Research from the Warehousing Education and Research Council suggests that optimised slotting can reduce travel time by up to 40%, yielding significant labour savings.
Receiving and Inspection Process
Establish a thorough receiving process that includes:
- Scheduled delivery windows to prevent dock congestion
- Immediate inspection protocols for incoming inventory
- Clear procedures for handling discrepancies
- Efficient putaway workflows to ensure stock availability
A structured receiving process ensures that your pick and pack operations start with accurate inventory, preventing downstream issues during order fulfilment. Our fulfilment software provides real-time visibility throughout this process, from receiving to final shipping.
Technology Solutions to Enhance Picking Efficiency
In modern warehouses, technology plays an increasingly vital role in optimising pick and pack operations. Implementing the right tools can dramatically improve accuracy, speed, and visibility.
Barcode Scanning and Mobile Devices
Barcode systems represent the foundation of accurate warehouse operations. By scanning products during picking, staff can verify they’ve selected the correct item, reducing error rates by up to 67% according to studies by the Aberdeen Group. Mobile scanning devices allow for real-time inventory updates and paperless workflows.
Advanced Picking Technologies
For warehouses ready to increase efficiency further, several pick-and-pack automation options exist:
- Pick-to-light systems: LED displays guide pickers to the correct locations and indicate quantities needed.
- Voice-directed picking: Headsets provide verbal instructions, allowing hands-free operation.
- Put walls: Illuminated compartments organised by order for efficient sorting during batch picking.
These technologies can increase productivity by 30-50% while simultaneously improving accuracy.
Warehouse Management Systems
A robust Warehouse Management System (WMS) serves as the brain of your operation, coordinating all pick and pack activities. Cloud Fulfilment’s software integrates with major eCommerce platforms, providing:
- Real-time inventory visibility
- Optimised picking routes
- Performance Analytics
- Order status tracking
- Automated documentation
Cloud Fulfilment’s software integrates with major eCommerce platforms, providing: Real-time inventory visibility, optimised picking routes, Performance analytics, Order status tracking, and Automated documentation. Additionally, our in-house IT expertise allows for customised reporting and process optimisation, and our access to the Parcel Monkey Group’s broad network of global couriers allows for competitive international shipping. Implementing pick-and-pack solutions powered by sophisticated software allows businesses to scale operations without proportionally increasing labour costs. Our order fulfilment software provides these capabilities while remaining user-friendly and adaptable to specific requirements.
Packing Best Practices for Speed and Accuracy
While picking often receives the most attention, efficient packing procedures are equally important for successful order fulfilment. The right approach to packing ensures products arrive safely while optimising both materials and labour.
Packing Station Setup
Well-designed packing stations should include:
- Adjustable work surfaces at ergonomic heights
- Easy access to a variety of packaging materials
- Integrated scales for accurate weight calculation
- Label printers positioned for efficiency
- Adequate workspace for order assembly
The goal is to create a workspace that minimises unnecessary movement and prevents fatigue during repetitive tasks.
Packaging Selection and Materials
Choosing appropriate packaging involves balancing protection, cost, and environmental considerations:
- Use standardised box sizes where possible to simplify the selection
- Consider poly mailers for soft goods that don’t require rigid protection
- Implement on-demand packaging systems for custom-sized boxes
- Select environmentally responsible void-fill materials that provide adequate protection
For specialised items, custom packaging solutions may be necessary. Cloud Fulfilment’s pick and pack services include knowledge in industry-specific packaging requirements, from fashion items requiring special handling to fragile beauty products needing extra protection.
Quality Control Integration
Incorporate verification steps within the packing process:
- Final scan confirmation of all items
- Visual inspection for product condition
- Verification of special instructions or gift options
- Weight-based checking to identify missing items
A systematic approach to quality control at the packing stage catches errors before they reach customers, protecting brand reputation and reducing costly returns.
Key Performance Indicators for Measuring Success
Implementing picking and packing best practices requires ongoing measurement and evaluation. By tracking the right metrics, you can identify improvement opportunities and validate the impact of changes.
Essential Pick and Pack Metrics
Key indicators to monitor include:
- Order accuracy rate: Percentage of orders fulfilled without errors
- Pick rate: Number of items picked per hour
- Cost per order: Total labour and materials cost divided by order count
- Cycle time: Time from order receipt to shipment readiness
- Fill rate: Percentage of orders shipped complete on first attempt
Warehouse managers should establish benchmarks for these metrics based on industry standards and company-specific goals.
Continuous Improvement Process
Use performance data to drive ongoing optimisation:
- Establish current baseline performance
- Identify the most impactful areas for improvement
- Implement targeted changes
- Measure results and adjust accordingly
- Repeat the cycle regularly
This systematic approach ensures that pick and pack warehouse operations evolve to meet changing business needs and maintain competitive advantages.
Benefits of Outsourcing to a 3PL Pick and Pack Provider
For many businesses, particularly those experiencing growth or seasonal fluctuations, outsourcing pick and pack fulfilment to a third-party logistics provider offers significant advantages.
Cost Efficiency
Outsourcing eliminates major capital expenditures:
- No warehouse lease or purchase costs
- Reduced equipment investment
- Flexible labour costs that scale with volume
- Shared technology infrastructure
These savings allow businesses to convert fixed costs to variable expenses that align with actual needs.
Scalability and Flexibility
Working with a 3PL provides built-in scalability:
- Handling of growth without operational disruption
- Capacity for seasonal peaks without year-round overhead
- Geographic expansion without additional facilities
- Access to established carrier relationships and volume discounts
Cloud Fulfilment’s UK-based pick and pack services provide the flexibility high-growth businesses need, with systems designed to scale alongside operations.
Focus on Core Business
Perhaps most importantly, outsourcing logistics allows business leaders to concentrate on growth initiatives rather than operational challenges:
- Direct management attention to product development and marketing
- Reduce time spent on logistics recruitment and training
- Leverage logistics expertise without developing it internally
- Improve cash flow through reduced inventory investment
Many successful eCommerce businesses find that outsourcing order fulfilment becomes a strategic advantage rather than merely a cost-saving measure.
Optimising the pick and pack process represents one of the most impactful improvements for order fulfilment operations. By implementing the right picking method, organising the warehouse strategically, leveraging appropriate technology, and measuring performance consistently, businesses can achieve significant gains in both efficiency and customer satisfaction.
For businesses experiencing growth or seeking to improve logistics capabilities, partnering with an experienced 3PL offers a path to effective picking and packing best practices without the associated capital investment. Cloud Fulfilment’s scalable and competitively priced pick and pack systems provide the infrastructure and knowledge needed to support business objectives.
To learn how optimised picking and packing can benefit specific business needs, visit our fulfilment pricing page and review solutions tailored to your requirements.
Frequently Asked Questions About Pick And Pack Best Practices
What is the pick-and-pack policy?
A pick-and-pack policy outlines the standard procedures, quality expectations, and performance standards for warehouse operations. It typically includes guidelines for order prioritisation, accuracy requirements, packing standards, and error resolution protocols. Developing a comprehensive policy helps maintain consistency across staff and shifts while providing clear metrics for performance evaluation.
How can I be a better order picker?
Improving individual picking performance involves both skill development and smart work habits:
- Learn the warehouse layout thoroughly, including product locations
- Understand how to efficiently use scanning and inventory management tools
- Practice proper lifting techniques to prevent fatigue and injury
- Develop a consistent rhythm to maintain productivity throughout shifts
- Request feedback and track personal metrics against targets
Many warehouses offer structured training programs to help pickers develop these skills systematically.
How to reduce picking and packing errors?
Beyond technology solutions, error reduction strategies include:
- Implementing the “touch it once” principle to complete each task fully before moving on
- Creating standardised procedures with checklists for complex orders
- Establishing quiet zones for concentration during verification steps
- Developing a peer review system for high-value or complex orders
- Offering incentives for error-free performance periods
These approaches foster a culture of accuracy that complements technological verification systems.
What makes Cloud Fulfilment’s pick and pack services stand out?
Cloud Fulfilment distinguishes itself through:
- Industry-specific knowledge in fashion, health and beauty, and other specialised categories
- Advanced software integration with all major e-commerce platforms
- Access to global courier networks for competitive international shipping
- In-house IT capabilities for customised reporting and process optimisation
- Scalable solutions designed specifically for high-growth businesses
These capabilities allow Cloud Fulfilment to offer tailored pick-and-pack solutions that adapt to business needs.